Vacuum Work Hold-Down Tray
Cutting paper in the laser can be challenging. The stock has to be held down uniformly across the surface, particularly if you are cutting small pieces out entirely. Otherwise, the air assist can move the cut-out bits around and, they can interfere with other cuts.
I mostly have been using Seklema hold-down mats for this. They have a sticky gel layer that holds the paper down without transferring any residue. They work really well but, they ablate with use and, are a bit expensive.
With some laser cutters, you can get a vacuum tray that holds lightweight materials like paper down with controlled airflow. There isn’t one of those for the Glowforge. So, I made my own.
This is heavily inspired by several other vacuum trays made by other Glowforge owners in this forum thread.
I designed this in Inkscape. I used a tabbed box generator for the two main bodies: the tray and the fan box. I modified the output to break the pieces into sizes I can cut in the Glowforge and, to add additional features like holes for the fan and electronics and channels for air flow.
The tray is 1/4” thick MDF. I lined the bottom with aluminum foil for extra protection in case any stray lasering gets through. It’s probably overkill but, I sealed the seams with silicone caulk to reduce air leaks. The cutting surface is a piece of perforated stainless steel plate sandwiched in an MDF frame. That is held down to the rest of the tray using magnets, with an EVA foam gasket to help with air leaks.
The fan box is 1/8” thick MDF with press-fit holes for the power connector and switch. The fan is bolted on to the end opposite the switch. This uses a 12v fan and a standard 12v power supply. The cord hangs out through the front of the lid of the machine.
I painted all the MDF black so it would look more finished and less cobbled together.
Cutting the plate steel without access to a shear was a new adventure for me but, worked out really well.
It works great, as you can see in the 1.6-minute demo video below.
Making of the Garden Lantern Electronic Pop Up Card
The Garden Lantern Electronic Pop Up Card I made in 2017 was one of the first big projects where I shot video documenting the build. There was a lot of footage and, I wasn’t very comfortable with editing videos at that point. The raw video just sat in a folder for a few years. I have done a bunch of build videos since then and, it occurred to me that I could probably manage to pull the old video clips together into a build narrative. I have been slowly putting that together in the last few weeks and, it is finally done!
As I noted in my original post about this project, this was inspired by and based on work done by Jie Qi and Natalie Freed. The Chibitronics Circuit Stickers project made everything a lot easier.
Powder Coat-Filled Laser Engraves
After seeing a video on powder-coat-filled laser engraves, I decided to try to adapt the technique for use with the studio Glowforge.
I temporarily blocked the air assist to keep it from blowing the fine powder around, which you can read more about by following the link.
The studio laser has a pretty potent external exhaust fan, which kept smoke from being an issue with the air assist restricted.
I wore a dust mask and gloves while working with the powder. I don’t think it is particularly toxic but, I’m sure I don’t need it in my lungs.
I did quite a few experiments on pre-finished 3mm maple plywood and clear acrylic. Initial results with normal initial engrave depth and, settings optimized to melt the powder coat were kind of a bubbly, uneven mess.
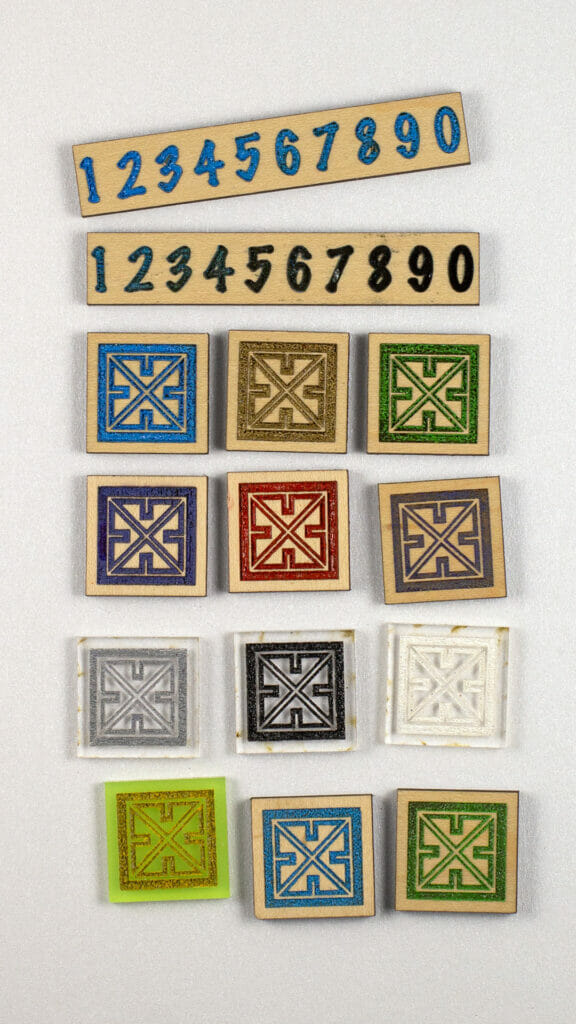
A pretty low power level will fuse the powder coat. A little more than that completely vaporizes it.
Increasing the resolution of the fusing pass helps a little, up to a point. Higher resolution delivers more energy to the fill and, also requires adjusting the power to compensate.
Giving the material a shallower channel improved things some. I switched to using half the standard power for the initial engrave, resulting in engraves about .4mm deep. The final result still had a lot of texture.

I finally hit on defocusing the laser for the fusing pass. While there is still some texture in the completed fill, it is a lot smoother.
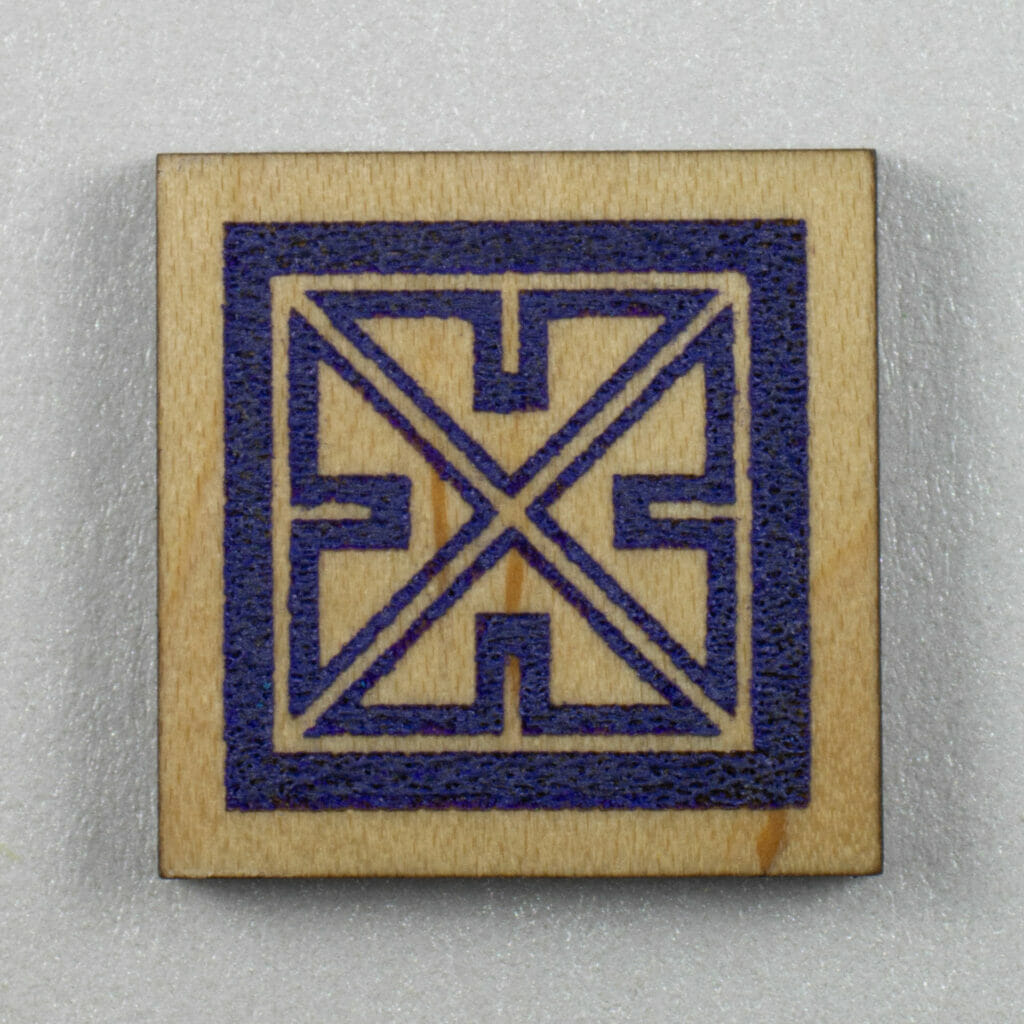
The general technique is:
- Pin the material down so it won’t move
- Do the initial engrave (at half-power for the normal material engrave)
- Dump some powder coat over the engrave
- Tap the powder into the engrave with a square-end paint brush
- Scrape the excess powder level with the surface of the material using something like an aluminum business card
- Run the engrave again with the poweder coat settings
Using masked material simplified clean up on the test pieces. The un-fused powder wipes off fairly easily or, comes off of the ply with a light sanding, though.
This produces a nice opaque saturated fill and, is available in a rainbow of colors and metallics. It also works great on acrylic.
Settings for Glowforge
Half-depth initial engrave (~.4mm)
1000 / 15 / 340 LPI
Focus for 1/8” stock: .2”
One-minute demo video:
Lasering Cactus Leather
I’m always interested in exploring more sustainable materials for making things. Awhile ago, I got a cactus leather sample kit from Desserto and, finally got around to trying it this week.
The samples range in thickness from about half a millimeter to 1.8 millimeters and, come with a different backing materials:
50% polyester / 50% cotton
65% polyester / 35% cotton
100% polyester
100% cotton
100% cotton “infused with cactus”
100% nylon
Some of the backing matches the material for color while others do not.
They also offer a number of different surface finishes.
The bolts are 1.4 meters wide and, run between $22 and $52 USD per meter, depending on the specific configuration.
Vaporized material seems to re-deposit as a sticky goo on the surface. Masking mostly prevents that and, the goo will wash off with some mild soap (I used a foaming hand soap) and a bit of rubbing. Isopropyl alcohol can take it off, too but, will also damage the finish noticeably in some cases.
I found the masked 1mm thick 50/50-blend-backed stuff cut at about 245 speed / 75 power on the Glowforge. I got decent (masked) engraves at 1000/51/270LPI.
Filling engraves with acrylic paint (via Posca-style pens) worked pretty well. The surface also takes paint acceptably. I bet it would screen print nicely.
I came up with a simple card case to make from one of the 10cm by 15cm samples.
I made a one-minute video summarizing all this:
As a bonus for those actually reading this post on my site, here is the pattern for the card sleeve (right-click, save link as to save the SVG).
Walnut Scouting Fleur-de-lis Pins
I had a whole bag of these Scouting fleur-de-lis walnut cut-outs left over from making Cailyn’s Challenge Coins. With a little sanding, some butterfly clasp pin backs, some glue and, some wipe-on poly, I turned a few into these nifty pins.

I made a one-minute making-of short:
Butterfly Knotwork Cards
There have been some inquiries about cards printed with some of my Celtic knotwork designs. I made up a small batch with the butterfly printed on some really nice bright white paper with a lovely “touch” (the way the card feels).
These are not Gocco prints, like the ones in the portfolio as those would have to be priced much higher. These look and feel really good, though.
The Knotwork Butterflies are up in the shop now, individually and, in packages of three (for less than the price of two singles).