Walnut Scouting Fleur-de-lis Pins
I had a whole bag of these Scouting fleur-de-lis walnut cut-outs left over from making Cailyn’s Challenge Coins. With a little sanding, some butterfly clasp pin backs, some glue and, some wipe-on poly, I turned a few into these nifty pins.

I made a one-minute making-of short:
Butterfly Knotwork Cards
There have been some inquiries about cards printed with some of my Celtic knotwork designs. I made up a small batch with the butterfly printed on some really nice bright white paper with a lovely “touch” (the way the card feels).
These are not Gocco prints, like the ones in the portfolio as those would have to be priced much higher. These look and feel really good, though.
The Knotwork Butterflies are up in the shop now, individually and, in packages of three (for less than the price of two singles).
Cailyn’s Challenge Coins
I made these walnut “challenge coins” for my niece to hand out at her Eagle Scout Court of Honor. A simple project on a tight timeline, I got 80 of these to her in time.
These are 1.5” diameter, cut from 1/4” thick pre-sanded walnut hardwood. I used the jig-in-place technique to align both sides of each coin. After engraving and cutting, they were sanded with 320 – 2000 grit sanding film, cleaned with my mini shop vac, wiped with a microfiber cloth, then coated with wipe-on poly. There was only time for one coat but, it contributed a lot to the final look.
I made a one-minute making-of short:
Spirals Bookmark Redesign
I designed a kirigami Spirals Bookmark last summer, mostly just taking what I did for one of my velvet embossing plates and, using that with minor changes. It was good but, there were a few spots where it was a little fragile – bits of connecting paper less than a millimeter wide.
More recently, I was inspired to redesign the spirals bookmark to make it a bit more robust. While I was at it, I made a few and, made a few of my Celtic key pattern design bookmarks and, put them all up in the new shop section. The designs are available individually, in three-packs and, in a variety pack with all three designs.
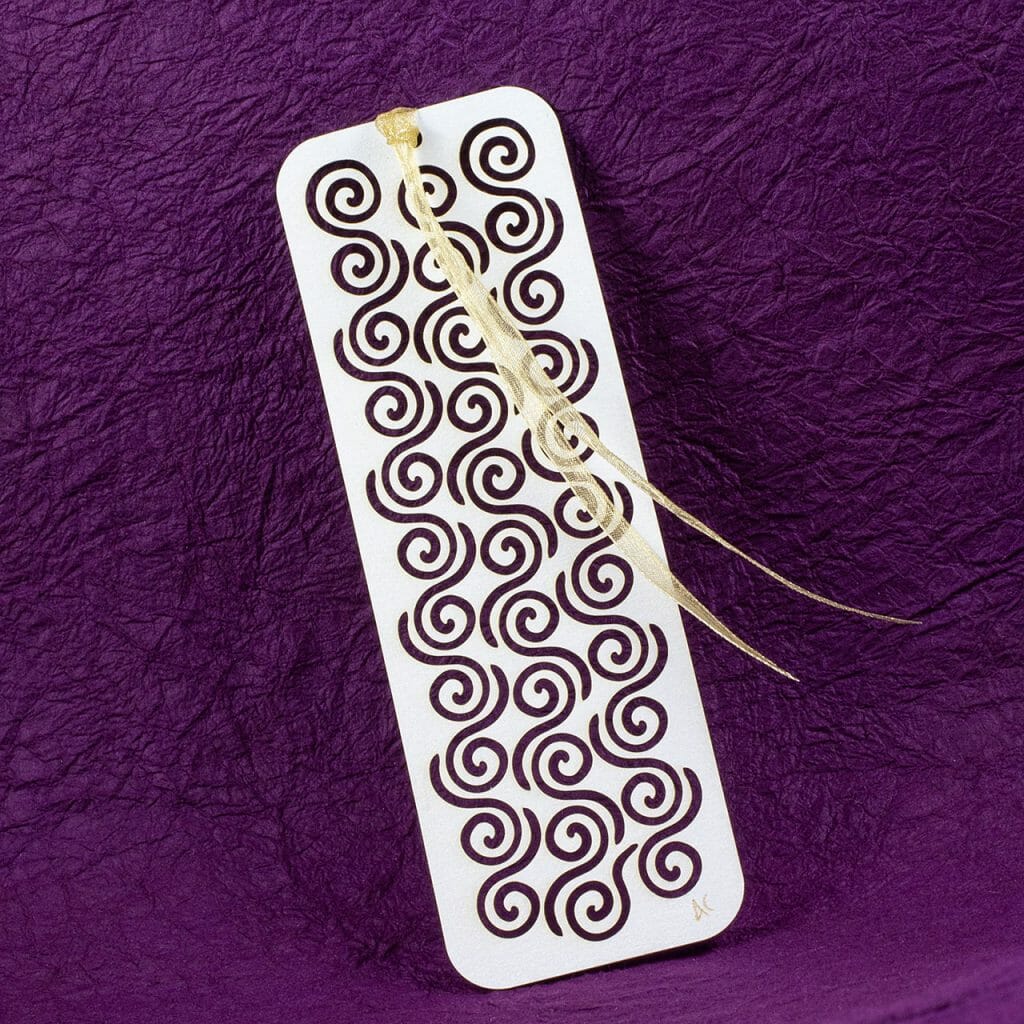
Auntie Tanya Kokeshi
The Auntie Tanya kokeshi is kind of a work-in-progress. My friend has three nieces and is her generation’s keeper of the family’s cultural traditions. I modeled this in Nomad Sculpt, 3D printed in nylon resin and, painted by hand (obviously … I need some more practice). I made a tiny azuma bukro out of retired kimono pieces and silk to wrap them. The dolls are about 75mm tall. Bottle cap for scale.
Celtic Key Square Wood Inlay Pins
Playing with some small-scale wood inlay this week, I made these Celtic key pattern pins. The key pattern and larger key square are 30mm x ~3mm thick. The smaller key square is 25mm x ~3mm thick. These are all hardwood maple inlaid with walnut. Everything is cut on the laser, sanded to 650 grit and, finished with wipe-on poly. I attached pin backings with wood glue.